Dst File Converter Embroidery
Embroidery design files can easily be converted to a file of one of the other formats (pes, dst, exp, pcs, hus, vip, shv, jef, sew, csd, or xxx). Follow the steps below. Open Design Database. In the folder pane, select the folder containing the embroidery design that you want to convert. In the contents pane, select the embroidery design file. Click File, the Convert Format.
From the Format Type selector, select the format. Under Output To:, select whether the new file is added to the same folder as the original files ( Same folder) or to a specified folder ( Following folder). To change the folder where the new file will be added, click 7. Click Convert.
The file is converted, and the new files is added to the specified folder.
Not sure what these people at Lids are talking about. I want to get a logo I made on Photoshop onto a blank hat, basically. They told me I need to 'digitize' the logo. Naturally, it is already digitized, just not the right format they need.
They said something about DMT or EMF. I prob have those completely backwards and wrong but they told me what format I needed. The only thing I know is that it is not a natural format in Photoshop. Lids has some pretty standard software that runs on Windows and I'm not sure what they use but if I did I could probably get somewhere. I was in the store today and didn't think to ask them to click on File Open to see what kind of files that the program would accept. I am sure they knew what they were talking about when they said 'DMT or EMF' (again, I haven't the slightest recollection of what they actually said) but it still might of helped to go that extra step.
Athelas regular. If anyone knows what I need to do, it would be great, as I am trying to keep everything uniform between my shirts, website, and hats. Click to expand.No. It is you who did not understand the answer. The logo must be in GIF or JPEG format. The one-time $50.00 fee is the setup fee to get your digital artwork into the embroidery machine.
Design format (Tajima).dst. This is a file for creating designer instructions for Tajima embroidery machines with set computerized control. It contains a set of codes and coordinates that control needle work, stops, laying seams or skipping sections. It contains data regarding vector formats and color pallets. The Data 7 Embroidery Design Conversion Tool can convert over 20 different embroidery design formats! - NOW including the American style Home Formats. It creates RGB and COL files compatible with Embird and Buzz Tools. It shows designs in a 1, 4, 9, and 16 grid for fast visual recognition.
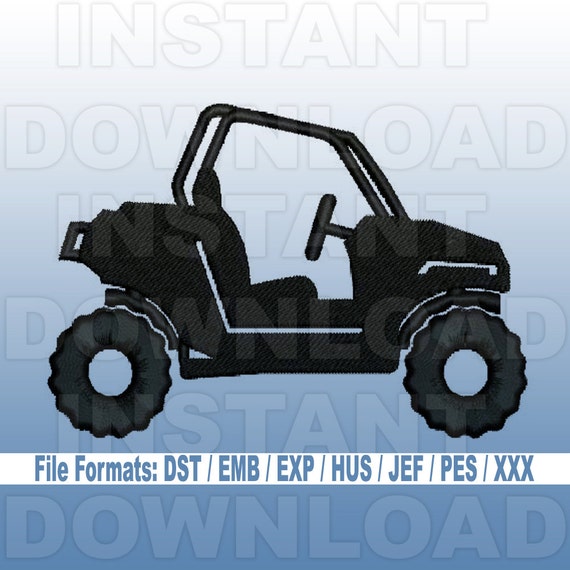
This fee is waived for orders of 36 or more. I gather from your response to citizenzen that you think that you can weasel your way out of the $50 fee by converting your artwork into the embroidery machine's format. I am afraid that you have another think coming. If embroidery is anything like every other professional graphic art, then then converting artwork from GIF or JPEG into the machine's format is only a small part of the setup. A little info from an artist who has worked with embroidery digitizers/embroiderers for around 10 years: When a logo or artwork is 'digitized' for embroidery, it is setup by someone who knows how to get the stitches to 'plot' correctly and most efficiently by the 'sewing machine.' It's not just changing it from one file format to another.
An embroidery program is used to digitally plan out pretty darn accurately how the thread will go onto the item. As in, all the stitches, thread changes, thread trims, etc.
Will be set up and previewed prior to the information being sent to the machine(s). There are different stitch types, stitch densities and lengths, and stitch directions used for different purposes that go into making artwork look and embroider best (not pucker, pull, draw up, etc.). The item material type, surface shape, and all sorts of things are taken into account.
The digitizing process only relates to the file format you provide in that they have to import your file into their embroidery software to start their work on it. Some embroidery software programs auto-digitize.to a degree at least; and most of those still require a knowledgeable person to tweak the trims, stitch types, thread changes, etc. Pretty much unless you are an embroidery digitizer, there's little to no chance that you have or will have access to the software to set up your own embroidery file that will be usable by the pro equipment most shops use. Thus, you provide whatever file format they can work with and they digitize it for you. You can get artwork digitized by many different companies/sources, possibly for cheaper than Lidz $50 fee.

Some digitizers work independently; some work for embroidery shops. In my experience, you're better off letting the company who will be embroidering your goods do the digitizing.
Dst File Format Converter For Embroidery
They know what particulars will work best with their equipment. If your separate digitizer provides a file they have to re-work, they may charge you the fee anyway. Unless you have embroidery digitizing software it will not sew. My software cost 2 grand.
You can get cheaper software for embroidery digitizing, maybe around 300 dollars. I do logos in corel draw and save as a vector image.
If I have a bmp or jpeg I use vector magic. Another 300 dollars. Then import into embroidery software. The embroidery machine is basically a cnc device. The software tells machine arms which way to move, which needle to use and when to cut thread. What type of fabric and what kind of stitch to use.
Go on you tube and watch some videos and then spend the $50.00. Just open the.jpeg in AI (Illustrator) and select 'Convert to outlines' and voila, you have a digitized vector ready for print. If the company you are dealing with does not accept this format then find a new company. The file format listed above (vector) is the industry standard for print on clothing (hats, t-shirts, uniforms etc.). I have dealt with numerous vendors/print companies that do clothing over the years and vectors have always been accepted and in fact recommended by them. I have never had a problem with a job using a vector file format. Just open the.jpeg in AI (Illustrator) and select 'Convert to outlines' and voila, you have a digitized vector ready for print.
If the company you are dealing with does not accept this format then find a new company. The file format listed above (vector) is the industry standard for print on clothing (hats, t-shirts, uniforms etc.).
I have dealt with numerous vendors/print companies that do clothing over the years and vectors have always been accepted and in fact recommended by them. I have never had a problem with a job using a vector file format. Click to expand.I'm willing to bet dollars to donuts that many user-submitted custom graphics cannot be rendered in thread in a form that anyone would find acceptable. This means that the professional embroider must re-create the customer's design as an acceptable visual approximation of the customer's design. For someone like you who has been doing this for a while, submitting designs that don't require modification may be second nature.
However, everything that the OP says indicates that he not have a clue about the difference between pixels on a computer screen and thread on cloth. I'm also willing to bet that his design proves it. Depends on how complex the logo is to get it right. The more simple logo, the better it looks. Normally, we take a jpeg copy of the image or scan one if the customer doesn't have a jpeg version.
The higher quality image of course makes it easier to stitch. There's software like Wilcom which our designer would use to 'stitch' it. There are others of course.
Once the design is done, it gets loaded to a machine which does the actual stitching. The machine could be plugged to a PC, via a usb port or sent to it via flash drive. We have a six needle machine that handles the stitching. Depending on how complex the logo is, and how big, it takes a few minutes to an hour. Bigger machines of course improve speed and quality of the work.
I'm willing to bet dollars to donuts that many user-submitted custom graphics cannot be rendered in thread in a form that anyone would find acceptable. This means that the professional embroider must re-create the customer's design as an acceptable visual approximation of the customer's design. For someone like you who has been doing this for a while, submitting designs that don't require modification may be second nature. However, everything that the OP says indicates that he not have a clue about the difference between pixels on a computer screen and thread on cloth. I'm also willing to bet that his design proves it. Click to expand.Exactly.
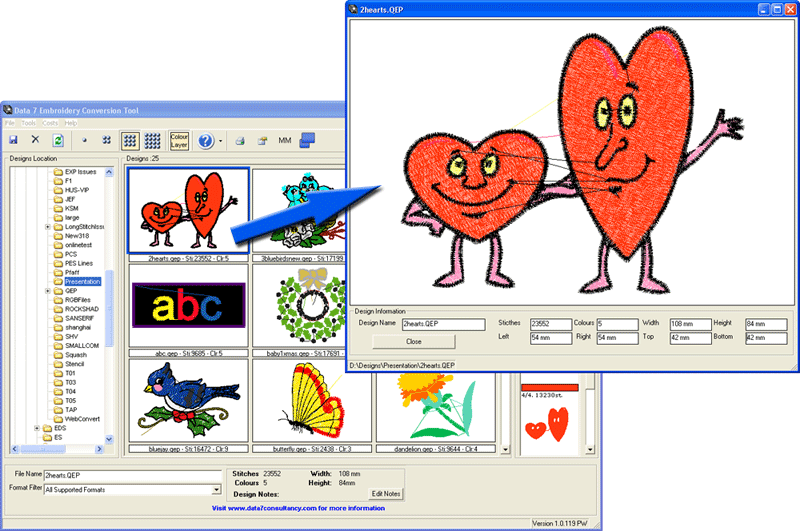
It does take practice to do it. In my experience, there are stitching programs that make you work harder, like you have to know which kind stitch to use or where the needle should go, stuff like that. That kind takes you months to really grasp it. Software like Wilcom's for example (there are others out there but that's the one i've used), make it like it is photoshop and 'dumb' it down a lot. A lot of things get automated so the output is a lot better for less time/effort to do it.
Software also makes stitching design faster/easier. I used to digitise design for embroidery machines in the family business years ago when I was going through uni. Back then we used a digitiser tablet with a puck to plot the design into software on an Atari ST. These days you can start with an electronic image.
Stitching embroidery is not like spraying ink on page. It requires a lot of thought.
There are different types of stitches and different fill densities to consider. If you are doing commercial quantities you want to minimise the number of thread changes as they slow production down whilst considering the order that the stitches need to be laid down. You need to think about the type of fabric the design is going onto. If it has a heavy weave your stitches might disappear if they line up in the same direction. You need to avoid stitching over the same area multiple times otherwise the thread keeps on breaking and the machine operator will hate you. The design might need to be simplified - that tiny text that looks fine in print might look horrible when converted to tiny little stitches.
Jpeg To Dst File Converter
Bottom line, it's not just converting from one file format to another. Someone has to put some thought into how to do it. You cannot do it yourself. The question of ownership of the digitised file was always an interesting one. Generally the embroidery place doesn't make any money on digitising the design but make money on the embroidering so they don't want you taking the digitised file somewhere else. Either they have to charge more for the digitising or charge an extra fee if you want the file. Click to expand.In order to embroider any design on any article of clothing, you need to provide Lids with an outline of the artwork and a color print of the colors you want, if any.
Digitizing is different than giving a printer artwork. I have worked with several digitizing companies.
What Lids or any other company has to do is use their digitizing devise, which plots the design to be interpreted by the stitching machine. The plotter, 'digitizer', determines the number of thread lines needed to fill your design. A $50 fee is cheap compared to others. I have paid hundreds of dollars to get designs on t-shirts, jackets, hats, etc. Hope this helps. Digitize and set up for embroidery I never realized how much work it was to set up and get a file digitized until I worked in a place that does custom embroidery.
Once the file is sent out to a digitizer for conversion into a file that can tell the embroidery machine where and how to stitch, the embroidery shop needs to stitch out the file as often there are edits to be made because stitches do not always look exactly the same as a graphic image of a logo. You are using thread stitches and thin lines, you can't always get the curves or solid edges, depending on the design. So now they have the time taken to send your graphic off, get it back, and stitch it out, call you, show it to you, then likely send it back and do that all over again. Once you approve it, and pick out the colors you want as there is not always an exact match of colors. The staff time involved is more than people realize.
Then you have the time the machine is tied up doing your stitch outs for your approval. All this and we still are not to the point where your actual order is being put on your item. THIS is why there are set up charges. The time it takes just to get ready to stitch out your order, the materials used, the emailing, and all the other things needed for normal processing. The terminology confuses people and the average person has no idea what all is involved. They don't see the rent, the utilities, and the many many other costs involved. I for one have a new appreciation and realize mark ups and service charges are NOT a way for businesses to gouge customers.
Many times we actually lose money because of the time involved. I tried using LIDS - and actually ordered from them - and it's been a nightmare. It's hard to understand from what the posted on their website, but it's actually a 6 business day production time. I ordered overnight shipping and they are telling me that the shipping will be an additional 7 business days.
Free Jpeg To Dst File Converter
They wouldn't cancel it because it's in 'production' where it has been for 3 days. I'm going to dispute it on my credit card. In the meantime, I went to a small local store and they did exactly what I wanted in 18 hours and charged me about the same as LIDS. They took my.GIF logo and digitized it for $60.
I'd guess they'll ship, but it's a great option if you are in LA. I'm sure every town has a similar operation and you'll likely get same or better results with a much faster turn-around.